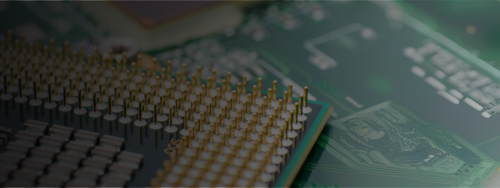
The semiconductor industry is experiencing exponential growth, driven by advancements in artificial intelligence, high-performance computing, and the ever-growing demand for connected devices. As this industry continues to expand, it is also confronted with an array of challenges—from the increasing complexity of component designs to stricter requirements for contamination control, process reliability, and cost efficiency. To stay competitive, manufacturers must navigate a dynamic landscape where precision, material performance, and scalability are paramount.
According to industry forecasts, the semiconductor market is expected to reach unprecedented growth levels, making it a crucial area for innovation and investment. However, this rapid evolution also underscores the need for robust, reliable solutions that address the unique demands of modern semiconductor manufacturing processes.
Growth in memory bit density and logic transistor counts.
As chip designs become more sophisticated, manufacturers are under pressure to meet higher performance standards and reduce defect rates while maintaining production efficiency. The trend toward smaller chip sizes, now pushing below 2 nm, brings unique challenges, such as the need for coatings that offer low particle counts, superior corrosion resistance, and minimized contamination. Traditional thermal spray methods are no longer sufficient for meeting these stringent demands. Instead, thin-film solutions such as Physical Vapor Deposition (PVD) and Plasma-Enhanced Chemical Vapor Deposition (PECVD) coatings have become increasingly critical.
The primary pain points for semiconductor producers include:
Oerlikon addresses these challenges by offering a wide range of advanced surface solutions that improve performance, durability, and reliability across various semiconductor applications. Our expertise in PVD, PECVD, thermal spray technologies and additive manufacturing allows us to provide targeted solutions for critical components, including electrostatic chucks, chamber liners, showerheads, and wafer handling systems. These offerings deliver several benefits:
Our thin-film coatings, such as BALINIT® DYLYN and BALINIT® DLC, are designed to reduce particle generation, enhance wear resistance, and provide exceptional chemical stability. This is particularly vital for components exposed to aggressive etching processes or where maintaining cleanliness is a top priority. By lowering defect densities and enhancing component longevity, these coatings ensure consistent high yields even as geometries shrink.
Our thermal spray guns are the premier solution for applying our high-quality powders in semiconductor applications. Engineered for precision and reliability, these guns deliver coatings with excellent adhesion and minimal porosity, making them ideal for critical components exposed to corrosive environments. By using our advanced thermal spray technology, manufacturers can protect chamber parts, heater plates, and shields, enhancing component longevity and reducing contamination risks.
Additive manufacturing (AM) enables the creation of complex geometries that optimize thermal management and fluid flow in semiconductor equipment. This technology is revolutionizing the design and production of components like cooling manifolds and gas delivery systems, offering enhanced functionality, reduced weight, and improved thermal performance.
By combining these capabilities, Oerlikon delivers a holistic approach to surface engineering that not only improves component performance but also contributes to overall process efficiency and sustainability.
Oerlikon’s global network of cleanroom coating facilities, deep material science expertise, and long-standing relationships with major semiconductor OEMs make us a trusted partner for the industry’s leading innovators. Our solutions are tailored to meet the specific needs of semiconductor applications, ensuring that manufacturers can confidently push the boundaries of what’s possible. As the semiconductor industry continues its trajectory of exponential growth, Oerlikon remains committed to providing the technologies and support needed to address today’s challenges and shape the future of semiconductor manufacturing.
© Copyright 2025 OC Oerlikon Management AG
Back to top keyboard_arrow_up