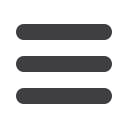
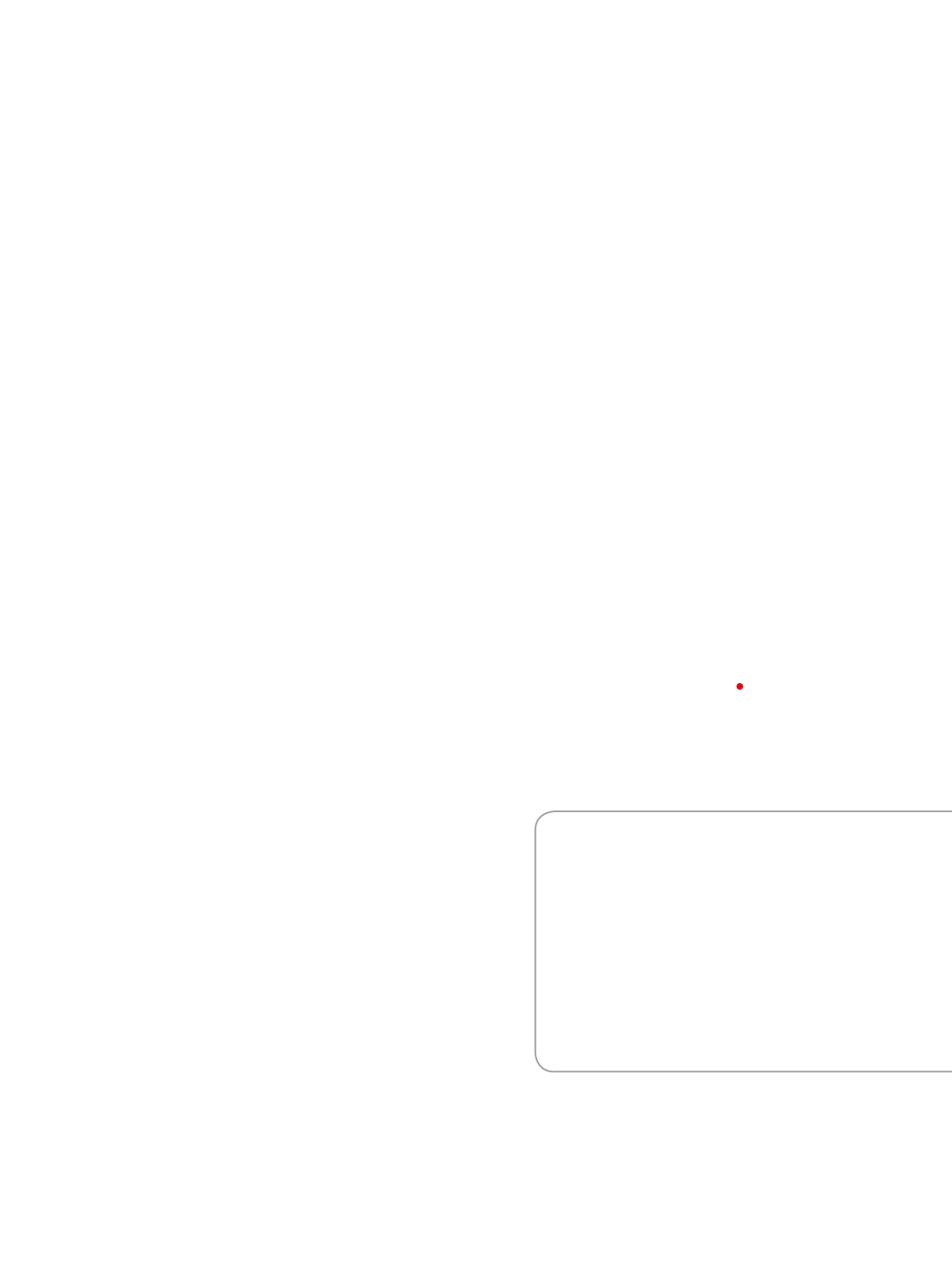
Passion
31
BEYOND SURFACES
Spring
16
fuel and air are mixed and introduced into the cylinders,
where they are ignited. The controlled explosion push-
es the cylinder down, both allowing the gas to escape
and pushing a linkage to the drive shaft so the vehicle‘s
wheels will turn.
The coating makes the difference
The coating must be applied inside the 918‘s eight cyl-
inders. The process takes on a new order of difficulty
because cylinders are precision machined into an alu-
minium engine block. After application, the coating is
machined by honing to ensure the correct diameter, de-
gree of roundness, and surface roughness needed by
the cylinders. The coating must also bind permanently
to the cylinder walls. “We wanted to choose an available
coating approved in mass production with minimal fric-
tion,” said Walter Buck, Porsche‘s project leader for the
918 powertrain.
The use of cylinder coatings in vehicles is well estab-
lished. For example, Oerlikon Metco, which was a tech-
nology partner for the special project team created to
make Porsche 918 Spyder a reality, has developed such
cylinder bore coating technologies for 20 years. Automo-
bile and truck manufacturers in Europe, Japan and in the
US rely on the products and systems.
Basic to the technology is a plasma depositing pro-
cess called an atmospheric plasma spray, or APS. The
plasma heats the coating powder materials above the
melting point and turns them into a molten stream that
can then be deposited through special spray equipment
onto the interior surface of the cylinders. The process
does not require the use of volatile chemicals as a carrier,
and so is more eco-friendly than other coating technolo-
gies. “The APS process offers the maximum variability in
the coating composition and is best suited to optimally
satisfy the engine specific challenges,” Buck said.
“Depending on the engine type, manufacturers have
various things they‘re looking for,” said Dr Peter Ernst,
Head of SUMEBore technology at Oerlikon Metco.
“Most are looking for low friction that will help them re-
duce emissions. Some of our customers have a corro-
sion problem, depending on fuel quality and the way the
engine is run, especially in the trucking business. Some
manufacturers want to increase the longevity of their en-
gines by reducing the wear. It depends on the customer
and the application what they are looking for.”
Deciding on exactly what coating to use is not neces-
sarily easy. Different engines will vary in the metallurgical
composition of their engine blocks and cylinders and the
way the coatings can interact with the system‘s opera-
tion. Porsche worked with Oerlikon Metco for nearly five
years, trying different variations and testing the results
to find a balance between pushing performance and yet
helping the engine to run 100,000 to 200,000 kilometres
without a problem.
Porsche eventually decided on an Oerlikon Metco
coating called Metco F4301. The specific composition
of F4301 with high amount of molybdenum improves the
coatings resistance to wear and scuffing and reduces
the friction. Although molybdenum is often an alloy com-
ponent in steel, here pure molybdenum is present as ‘is-
lands’ to create the unique properties Porsche is looking
for.
High-end technology for the mass
markets
But for all the technical details, at the end it is important
to focus on what they enable. The research and develop-
ment that helps allow a jet-like ride in one of the fastest
cars on earth eventually find their way into mass market
applications, or as improved engine longevity in a truck
or reduction of emissions in a common passenger car.
This is just another way that microscopically thin coat-
ings make life better for everyone.
“Porsche doesn’t just want to
offer an exciting driver experi-
ence, but also to make even
the highest performance vehi-
cles more eco-friendly.”
Dr Frank-Steffen Walliser, Vice President of
Motorsport at Porsche AG