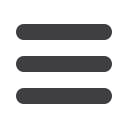
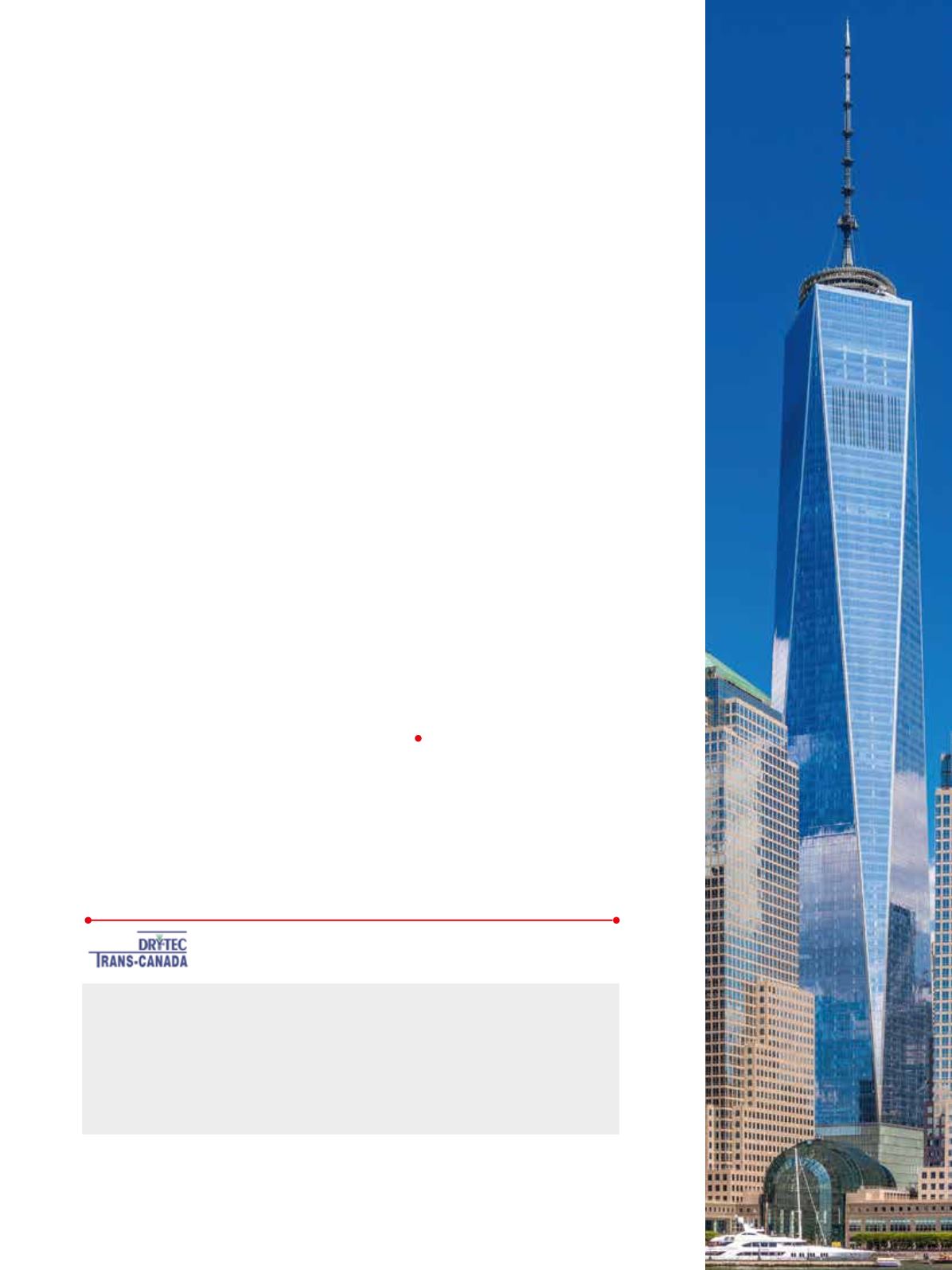
11
BEYOND SURFACES
Spring
16
Seventeen sections to objective
Having found the right process, the work could start. The
lower six spire sections were too bulky and too heavy to
be transported, so Drytec rented a hangar near the port
to perform the final metallization. The individual sections
were delivered in three parts and welded together on site.
The application of the zinc corrosion coating required the
simultaneous use of three wire combustion spray guns.
Drytec kept six of these guns on hand at all times to en-
able any necessary maintenance to be performed with-
out disruption to the coating process.
Seventeen sections, some comprising nested tubes,
had to be zinc-coated. For some, hard-to-reach areas,
an extension module – the Oerlikon Metco XT6-18T
45-degree-tilt angle spray gun – was needed.
Absolutely convincing
Especially challenging was the narrow available time win-
dow between abrasive grit blasting and the application
of the zinc coating, due to the rapid corrosion of high-
strength steel: the coating had to be applied within four
hours after grit blasting. Drytec used a total of 11,500 kg
of zinc wire to coat the 139.6 metre high spire.
The Key Account Manager likes to recall the City In-
spector’s reaction to his presentation: “He said to me: I
don’t want to have to climb up there with a can of paint
in a few years time to touch up the structure! If one of
your customers should ever doubt the quality of this pro-
cess, just tell him that the spire of the World Trade Center
was coated using a Metco 16E and zinc wire.”
DRYTEC Trans-Canada
The company with headquarters in
Quebec (Canada) is a specialist
provider of services in the area of
surface treatment and corrosion
protection. As well as standard
services, it also offers special coating
solutions for complex steel compo-
nents. In 2013, Drytec was commis-
sioned to corrosion protect the
139.6 meter high spire of One World
Trade Center.