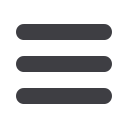
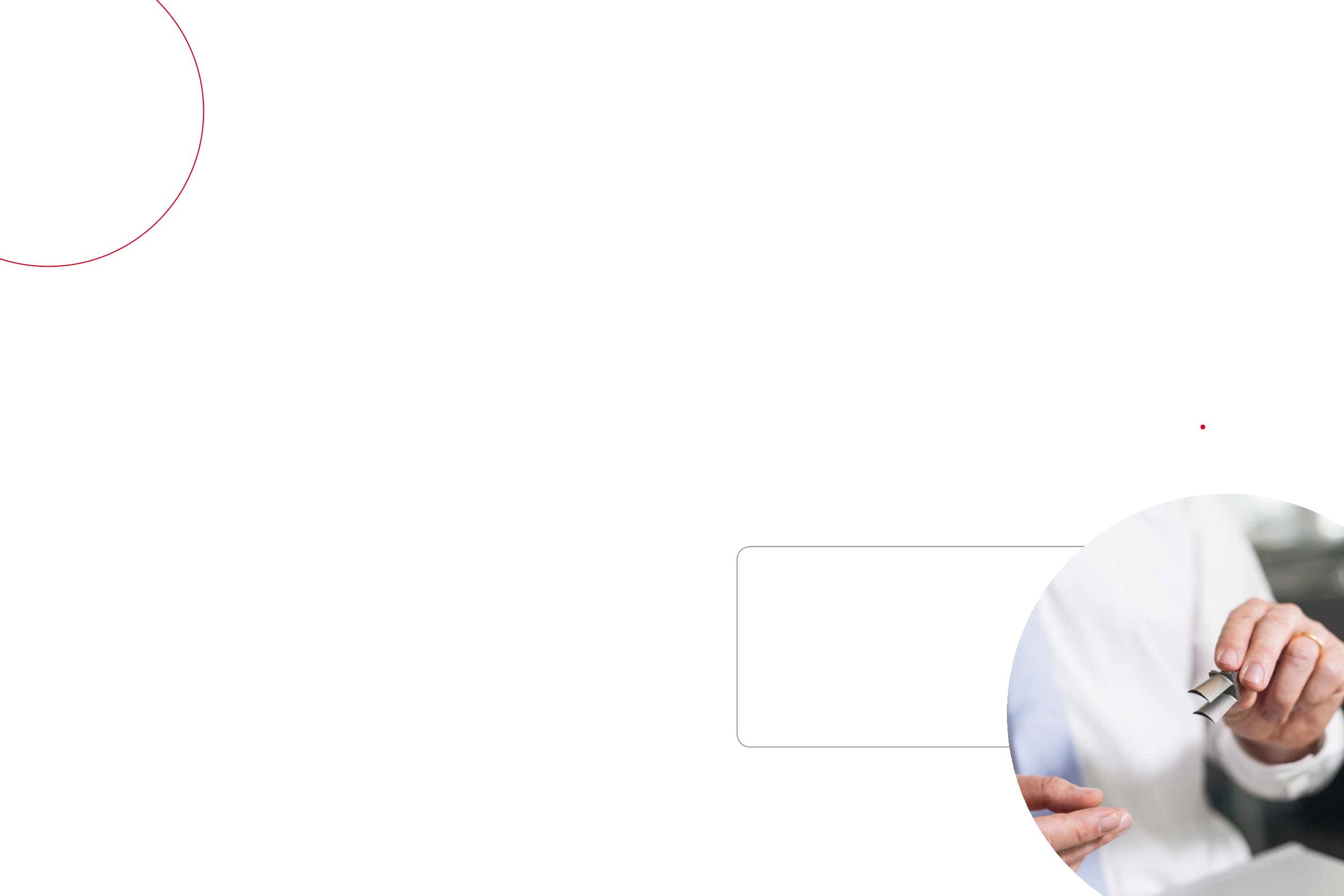
BEYOND SURFACES
Fall
16
26
Passion
it will also alter the manner in which
industrial processes and manufacturing
are carried out. The AM processes give
you more latitude in terms of design
and shape. While the slogan yesterday
was: “Design for Manufacturing,” today,
thanks to AM, we can say: “Design
for Function.” This is what makes
additive manufacturing so revolutionary.
When does additive
manufacturing make sense?
There are many areas. A classic
example is the area of one-off parts or
spare parts. If these are produced by
means of additive manufacturing, repair
times can be shortened and resource
intensive warehousing can be avoided.
But we are already one step
further, because the technology is
increasingly becoming established in
the manufacturing industry where it
complements conventional fabrication
processes. Individualized one-off parts
and small series can be produced this
way more promptly and more locally
for the customer. Instead of producing
centrally and sending things halfway
around the world in containers or by
air freight, the future will see us simply
sending the data to the printer which
then accurately prints out the needed
part in a short time right on site. And
if an apparatus with the desired
specifications is not yet available
at the moment, then it, too, will be
printed in the foreseeable future!
Another, significant advantage is
also that industrial components can
be manufactured quickly and in an
uncomplicated manner in new and
complex forms that previously were
only possible with great effort and
expense – even, in fact, using new
materials that were previously not
possible. Ultimately, this will further
improve the performance of products
and reduce the costs. And, by the way,
these are not just visions of the future.
Parts printed in series are already in
common use in aircraft, for example
in jet engines or control mechanisms.
You have mentioned the costs
several times now. How can
these be reduced through the
use of additive manufacturing?
There will be several possibilities
here. A significant difference between
additive manufacturing and previous
manufacturing processes is that
material is not removed or cut off, but
instead added layer by layer exactly
where it is needed. This saves material,
which makes the production more
sustainable, and, of course, for ex-
pensive metal-based materials, this
has a noticeable effect on the costs.
But there will also be savings in
the logistics chain and warehousing
when spare parts are only produced
on site when needed. However, to get
that far, the productivity of additive
manufacturing must still be improved
greatly, meaning the costs must go
down. This will be achieved through
more efficient machinery, automated
processes, reduced material costs and
new procedures. Today, a good deal
still takes place manually in this process.
Viewpoint
What is additive manufacturing
being used for already today and
what will the future look like?
The core application areas on which
we are concentrating have to do with
the manufacture of key components
for the aerospace, automotive and
medical sectors as well as for custom-
ers in the area of toolmaking and in
industrial production. We are already
working on customer projects in all
of these areas. Moreover, we are also
using additive manufacturing to fabri-
cate our own products – in the area of
thermal spray equipment, and for special
components for transmission solutions
and textile systems. Although these
projects are still in the research and
development phase, we will also pass
this knowledge on to our customers.
What are you working on right now?
In order to move the industrialization
forwards, it is especially important
to increase the productivity of the
process and expand the range of
materials. These are our main topics.
As a technology partner for key com-
ponents, we are working on developing
service centres where we can offer our
customers access to the production
of components by means of additive
manufacturing. We are also working on
improving the process technology and
the workflows. Our materials specialists
are also engaged in further expanding
our portfolio of materials for this area.
Are your customers already able
to work with the AM process?
Yes, we are already working on the
development of small series with various
different customers. And, because we
are going to expand our capacities
for printing, we will soon be able to
offer our customers manufacturing of
3D products globally as a service.
Mr Mauerer, thank you
for the interview!
“There is hardly a
technology at the
moment which offers
more potential
for growth.”