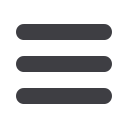
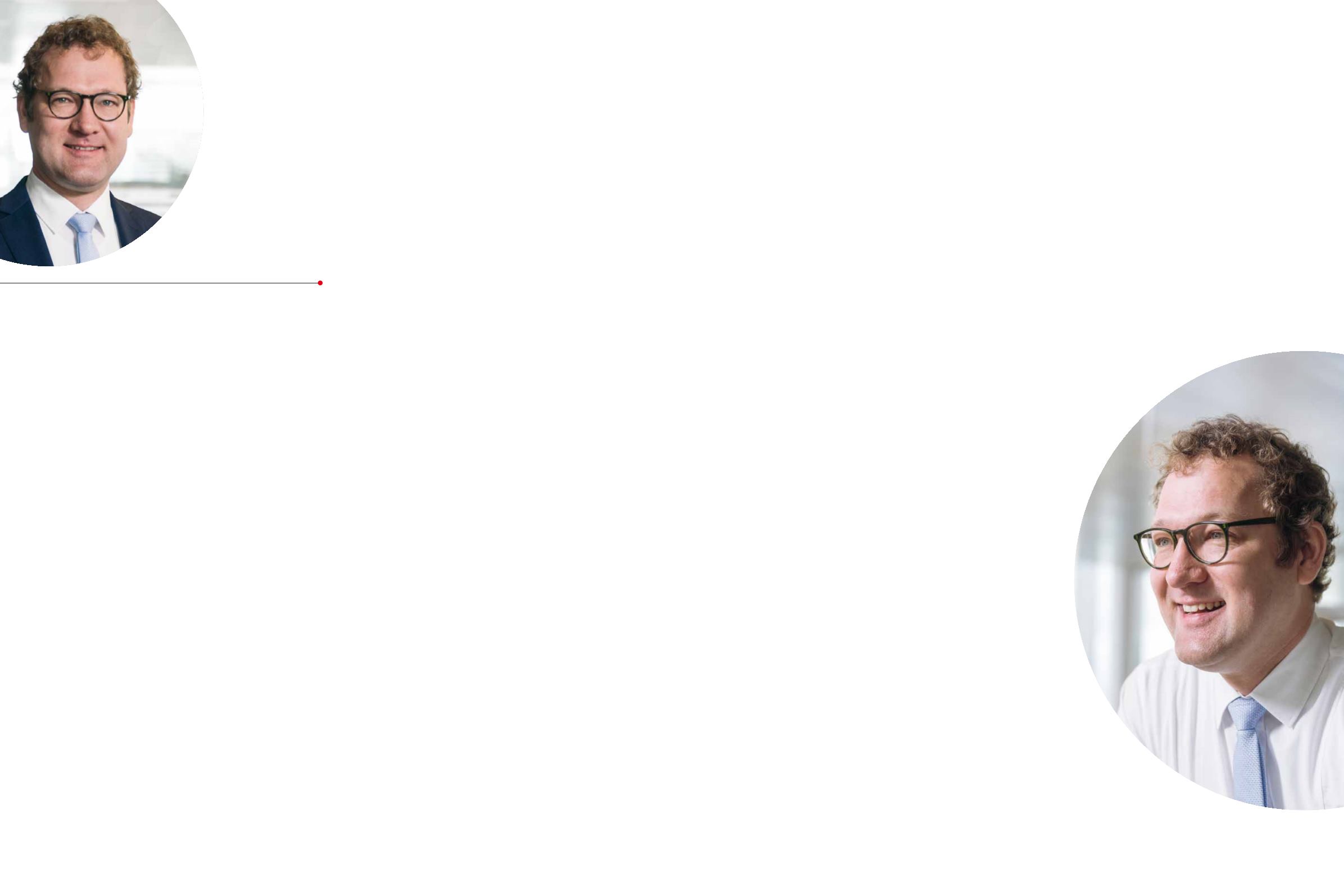
25
BEYOND SURFACES
Fall
16
24
Passion
Why is Oerlikon getting
involved now as well?
The great potential we see for additive
manufacturing lies in the area of
industrial fabrication. The manufacture
and processing of key industrial
components is part of our company’s
DNA. As a technology partner, we
are already serving leading industrial
enterprises in the area of modern
materials and coating technologies.
That means we are already
present today in two of the three
most important work steps: our
two brands, Oerlikon Balzers and
Oerlikon Metco are leaders with
their coating technologies for the
final processing of components. And
what’s more, Oerlikon Metco is also a
specialist in working with metal-based
materials. In addition, we have a wealth
of know-how to draw on concerning
process technology for the manufacture
of key industrial components.
Our aim is to build on these unique
areas of expertise and to be active
at the very forefront in shaping the
industrialization of additive manu-
facturing. We are presently rapidly
expanding our know-how and capac-
ities in this area and are able to make
them available to our customers.
medical technology, for example), but
it is also possible to create products
that, with conventional means, have
been either impossible or very difficult
to fabricate up until now. The increas-
ing industrialization of additive manu-
facturing will not only promote
further innovative
advances,
Additive Manufacturing (AM), also known as 3D printing, has the
potential to significantly change the way manufacturing is done in
industry: The increasing industrialization of additive manufacturing
is altering the manner in which industrial processes are being
carried out. More and more companies are already experimenting
with 3D printing. Now, Oerlikon is also entering the AM business.
Florian Mauerer, Head of the Business Unit ‘Additive
Manufacturing’, provides some insights.
Viewpoint
Is the market actually ready for this?
I would say: The market is more than
ready. There is hardly a technology at
the moment which offers more potential
for growth. The aero industry, as a
driving force for highly complex and
safety-critical manufacturing, is currently
repositioning itself for the future.
The figures of the ‘Expert Commis
sion for Research and Innovation’ of
the German Federal Government
confirm this development, for exam-
ple. While the worldwide revenue for
additive manufacturing processes
(3D printers, materials, acces-
sories, software, services) was
3.07 billion US dollars in 2013,
it will already reach a volume
of 7.31 billion in 2016. And
by 2020, it will even grow
to 21.2 billion dollars –
a three-fold increase in
only eight years! A tech-
nological revolution has
begun here and we want
to be at its forefront.
You want to open the
way to additive manufac-
turing for your customers.
What is the advantage for
customers as compared to
conventional manufacturing?
To put it simply: Additive manu
facturing makes new and more
complex products possible, and
does so more inexpensively and faster
than with conventional production
processes. For one thing, with additive
manufacturing, mass-produced items
can be customized (I’m thinking of
Additive Manufacturing
On the way to
industrialization
Mr Mauerer, everyone is talking
about additive manufacturing.
What’s behind it?
Additive manufacturing is a process
for the fabrication of three-dimensional
workpieces. It’s also often referred to
as 3D printing. Up until now, it was
customary to fabricate workpieces out
of one solid block by removing material
through milling, drilling or grinding.
Additive manufacturing, however, builds
up a workpiece layer by layer. This
gives rise to entirely new possibilities.
But why is AM technology
the buzzword just now? After
all, 3D printing has been
around for quite a while.
That’s right. Additive manufacturing
has been around for a long time, but
the technology has enjoyed some
considerable successes just recently
and is making great strides forwards.
Previously, it was primarily used for
processing plastic, which is well-suited for prototypes, but has not
really become established for use
in industrial end products. Today’s
methods can also process metals,
which means we are on the threshold
of an important step: the industriali-
zation of additive manufacturing. This
is the reason the big companies are
now getting on board. Metallic 3D
printing is reaching a certain maturity
level at the moment and this makes it
interesting for industrial applications.