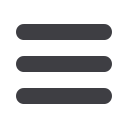
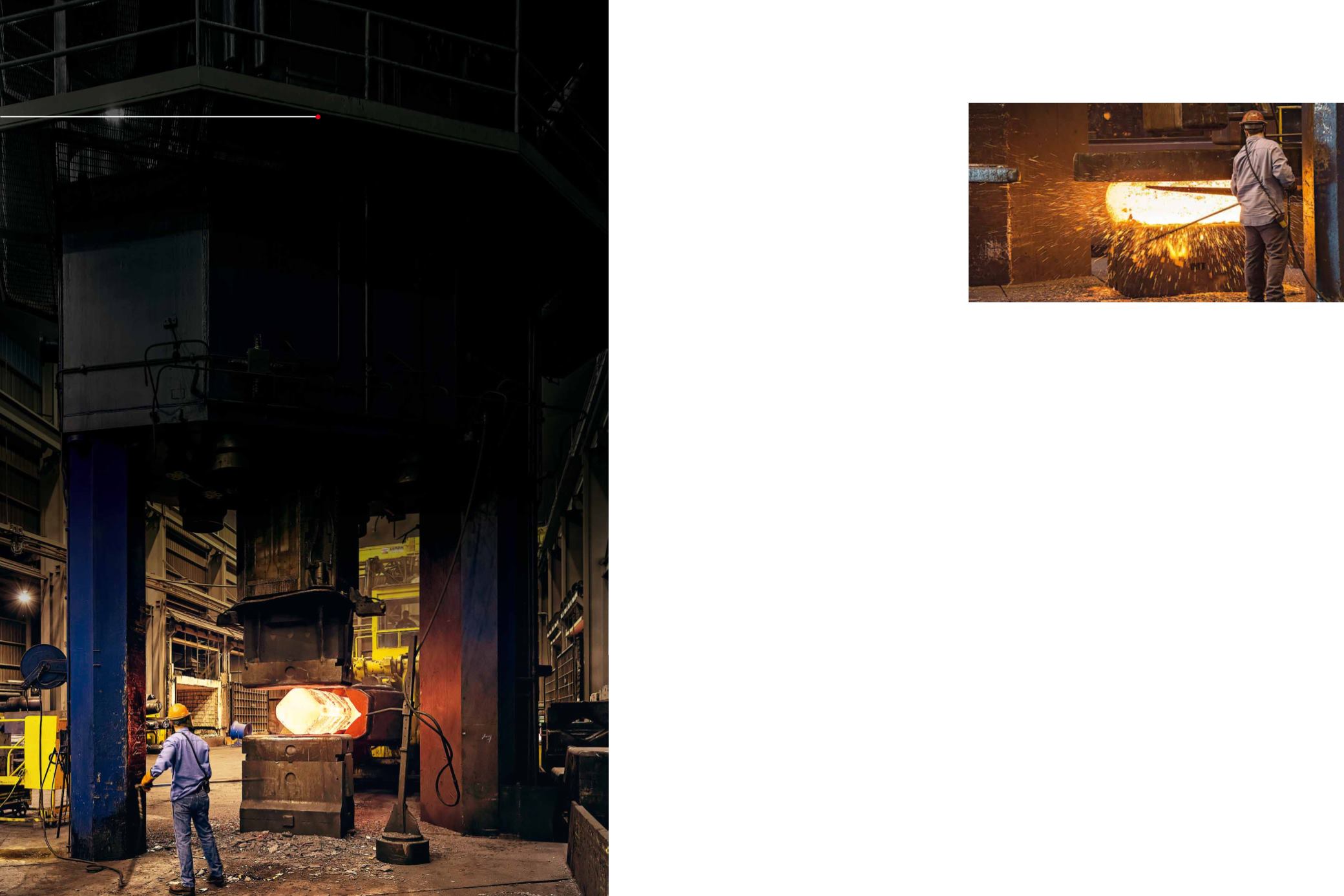
21
BEYOND SURFACES
Fall
16
Passion
A real
heavy hitter
16’500 US tons or nearly 15’000 metric tonnes: this is the almost un-
believable force generated by the new forging press from
Scot Forge, a specialist in the area of heavy-duty open-die forging.
It is one of the biggest presses in the world and didn’t only present
the developers at Scot Forge with a number of challenges, but also
the heat treatment experts from Oerlikon Balzers. This is because
the press’s four main cylinder rods alone each weigh 25 US tons
(22 tonnes) and thereby count amongst the biggest parts ever
treated by Oerlikon Balzers.
Scot Forge and BALITHERM IONIT
T
he largest press Scot Forge has manufactured
to date generates a pressing force of 6’300 US
tons (5’700 metric tonnes). Quite an amount – yet
still not enough for the increased demands the industry
is placing on Scot Forge’s heavy-duty presses. “We
wanted a press allowing us to process much more
complex parts than in the past. Anyone who played with
modelling clay as a child will easily know what we are
talking about: it’s really easy to form modelling clay into a
simple shape such as a cube; the more complex a shape
is, however, the more force one must apply,” says Laura
Diedrich, Scot Forge’s Marketing Specialist, explaining
the demands.
Scot Forge’s expectations regarding the performance
of its new heavy-duty forging press were soon clearly
defined; however, no provider seemed able to fulfil them.
“We therefore decided to develop our new press on our
own, as we do for most of our machines,” says Laura
Diedrich. The new press generates a force of 16’500 US
tons (15’000 metric tonnes), making it one of the biggest
open die presses in the world.
A jointly developed one-stop solution
In order to achieve the required level of precision and
other attributes – maximum wear resistance and shape
accuracy with minimal distortion – the engineers from
Scot Forge spent a long time tinkering about to find
the right coating for the press. Nitriding was soon dis-
cussed as a possibility, but the press parts were so big
that the use of conventional methods had to be ruled
out. “We joined the project very early in the planning pro-
cess, when the new press was still only on the drawing
board. The engineers from Scot Forge were just starting
to look around for ways to manufacture these enormous
parts,” explains Craig Reuter, Oerlikon Balzers Account
Manager in the USA. Under the joint direction of Roman
Gaida, Global Business Development Manager for Com-
ponents Nitriding at Oerlikon Balzers in Liechtenstein,
and the engineers at Scot Forge, a solution was devel-
oped which allowed even parts such as the four 25-tons
(22 tonnes) main cylinder rods and the 8.4-metre return
cylinder rods, each weighing 8.5 tons (7.7 tonnes), to
be treated. In the end we were able to offer Scot Forge
a one-stop solution, obviating the need to involve other
providers,” explains Roman Gaida.
BALITHERM IONIT, a process for the plasma nitriding
of steels, was developed by Oerlikon Balzers especially
for the surface treatment of large components. To
guarantee their safety throughout the entire process, a
high-frequency plasma generator was combined with an
automatic control system. The INAURA coating system
in which this process takes place can accommodate
components up to 10 metres long, 3 metres in diameter
and weighing up to 40 tonnes – enough space for the
different parts of the new Scot Forge press.
“The enormous parts of the Scot Forge press count
amongst the biggest components Oerlikon Balzers has
ever treated with BALITHERM IONIT. This presented
us with a new challenge: the standard fasteners were
unsuitable for the accommodation of the parts in